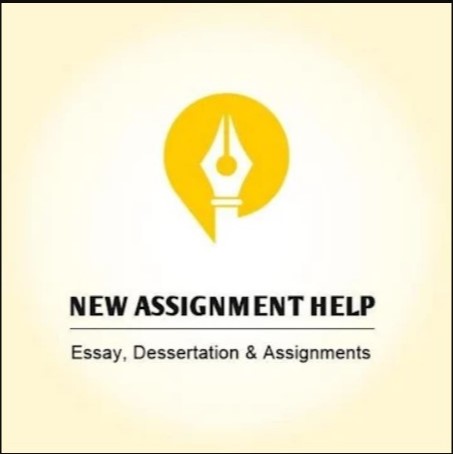
Get the best SPSS Assignment help and writing services online in UK by expert writer.
Optimizing Operations Management for Business Success
Operations management is a critical component of any business, responsible for ensuring efficiency, productivity, and the seamless delivery of goods and services. In today's competitive business landscape, Effective Affordable Operations Management Assignment Help in UK is more important than ever. This article will explore the key principles of operations management and how they can be applied to improve business performance.
Understanding Operations Management
Operations management involves the design, execution, and control of all processes that transform inputs into finished products or services. It plays a pivotal role in achieving the business's strategic goals and objectives.
The Importance of Effective Operations Management
1. Cost Reduction
One of the primary objectives of operations management is to minimize operational costs. By optimizing processes and resource utilization, organizations can reduce waste and achieve cost efficiencies. This not only increases profitability but also allows companies to offer competitive pricing to their customers.
2. Quality Improvement
Consistency in product or service quality is paramount in gaining customer trust and loyalty. Operations management emphasizes quality control, ensuring that products meet or exceed customer expectations. By implementing quality control measures, businesses can reduce defects and improve overall product quality.
3. Customer Satisfaction
Customer satisfaction is directly linked to efficient operations management. Quick and accurate delivery of products or services, as well as timely responses to customer inquiries, contribute to a positive customer experience. Happy customers are more likely to become repeat buyers and recommend the company to others.
Key Components of Operations Management
Process Design and ImprovementEfficient processes are the backbone of operations management. It's crucial to design and continuously improve processes to eliminate waste, reduce costs, and enhance product or service quality.
Capacity PlanningPredicting demand and matching it with the right level of resources is vital. Overcapacity leads to unnecessary costs, while undercapacity can result in lost opportunities.
Inventory ManagementEffective inventory management is essential for balancing supply and demand, minimizing carrying costs, and ensuring timely order fulfillment.
Quality ControlMaintaining quality standards and minimizing defects is critical to meeting customer expectations and reducing rework and waste.
The Role of Technology in Operations Management
Technology plays a significant role in optimizing operations management. Here are some ways in which it is leveraged:
Automation and RoboticsAutomation reduces human error, increases efficiency, and speeds up processes. Robotics can be used in manufacturing, distribution, and even customer service.
Data AnalyticsBig data and analytics help in making data-driven decisions, predicting demand, optimizing inventory, and improving overall operational efficiency.
Inventory Management SoftwareSpecialized software can help in tracking inventory levels, optimizing reordering points, and reducing carrying costs.
Supply Chain SoftwareSupply chain software can provide real-time visibility into the entire supply chain, enabling businesses to make better decisions and respond to disruptions quickly.
Lean Operations Management
Lean management principles focus on minimizing waste while maximizing productivity. This approach is widely used to improve operations. Key principles of lean operations management include:
Identifying and Eliminating WasteLean management identifies seven types of waste: overproduction, inventory, waiting, transportation, over-processing, motion, and defects. By eliminating these, businesses can operate more efficiently.
Continuous Improvement (Kaizen)Kaizen involves continuous improvement in all aspects of operations. Small incremental changes can lead to significant long-term improvements.
Just-In-Time (JIT) InventoryJIT systems reduce excess inventory and its associated costs by ensuring that materials arrive just in time for production.
Challenges in Operations Management
Despite the benefits, operations management faces several challenges:
GlobalizationManaging operations across borders and dealing with international regulations can be complex.
Supply Chain DisruptionsNatural disasters, geopolitical issues, and unexpected events can disrupt supply chains, affecting operations.
Changing Customer ExpectationsAs customer expectations evolve, businesses need to adapt to meet new demands and preferences.
SustainabilitySustainable operations management is a growing concern, as businesses need to balance profitability with environmental and social responsibility.
Case Study: Toyota's Lean Operations
Toyota is often cited as a prime example of successful lean operations management. The company's Toyota Production System (TPS) is renowned for its efficiency and quality. Toyota's success can be attributed to its focus on waste reduction, continuous improvement, and a culture of employee involvement.
Best Practices in Operations Management
To excel in operations management, businesses should consider these best practices:
Set Clear ObjectivesDefine specific, measurable objectives that align with the organization's overall goals.
Continuous ImprovementFoster a culture of continuous improvement to adapt to changing market conditions.
Cross-Functional TeamsCollaborate with various departments to ensure a holistic approach to operations management.
Invest in Employee TrainingWell-trained employees are better equipped to execute processes efficiently.
Regular Monitoring and ReportingImplement systems to monitor performance and generate reports for analysis and decision-making.
Conclusion
Operations management is the backbone of any successful business. By understanding its key components, embracing technology, adopting lean principles, and addressing challenges, businesses can optimize their operations to achieve greater efficiency, reduce costs, and meet customer demands. Through effective operations management, organizations can position themselves for long-term success in a dynamic and competitive marketplace.
FAQs
1. What is the role of operations management in businesses?
A: Operation management ensures that processes run efficiently, costs are controlled, and customer expectations are met, all of which are vital for business success.
2. Why is technology important in operations management?
A: Technology enhances efficiency and provides insights into operations, helping businesses make informed decisions.
3. How can assignments help benefit students in operations management?
A: Assignment help offers guidance, clarifies concepts, and ensures students submit high-quality assignments, leading to better academic performance.
4. What are the challenges in operations management?
A: Challenges include balancing cost and quality, supply chain management, and dealing with global operations.
5. What are the future trends in operations management?
A: Future trends involve the integration of technology, such as IoT and AI, to optimize processes and enhance efficiency.
喜欢我的文章吗?
别忘了给点支持与赞赏,让我知道创作的路上有你陪伴。
发布评论…