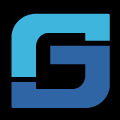
Nanjing Granuwel Machinery CO., LTD is specialized in R&D design and manufacture of high polymer extruders, and we concentrate our business.
The Ultimate Guide of Co-Rotating Twin Screw Extruder
Introduction About Co-Rotating Twin Screw Extruder
Co-rotating twin screw extruders have become the backbone of various industries, providing an efficient and versatile solution for material processing. From plastics to pharmaceuticals, their applications are vast and their benefits are manifold.
In the realm of material processing, the co-rotating twin screw extruder stands out as a game-changer. But what exactly is this marvel of engineering, and why is it gaining widespread adoption in industries worldwide?
Definition of a Co-Rotating Twin Screw Extruder
A co-rotating twin screw extruder is a sophisticated piece of machinery used for processing a wide range of materials by forcing them through a set of intermeshing, co-rotating screws. This process results in efficient mixing, melting, and shaping of the material, making it a preferred choice in various manufacturing processes.
Components of Co-Rotating Twin Screw Extruders
Screws and Barrels
The design and material composition of screws and barrels significantly impact the extruder's performance. High-quality, durable components are essential for ensuring longevity and consistent results.
Feed and Discharge Systems
Efficient material feeding and discharge systems contribute to the overall effectiveness of co-rotating twin screw extruders. Properly designed systems prevent material inconsistencies and ensure a smooth production flow.
Control Systems
Modern co-rotating twin screw extruders come equipped with advanced control systems. These systems allow operators to monitor and adjust various parameters in real-time, ensuring optimal performance and product quality.
Working Principle of Co-Rotating Twin Screw Extruder
Co-Rotating Motion Explanation
The co-rotating motion of the twin screws is a key element in the extruder's efficiency. This synchronized movement ensures thorough mixing and processing of materials, enhancing the overall quality of the output.
Twin Screw Design Advantages
Unlike single screw extruders, the twin screw design allows for better control over the processing parameters. The intermeshing screws create a shearing effect, generating heat that aids in the material's transformation.
Heat and Shear Effects on Materials
The controlled application of heat and shear within the extruder is crucial for processing materials with precision. This feature not only improves the material's consistency but also allows for the incorporation of additives and modifiers.
Importance of Co-Rotating Twin Screw Extruder in Various Industries
Industries such as plastics, food processing, and pharmaceuticals rely on co-rotating twin screw extruders for their unparalleled performance. The ability to handle diverse materials and provide precise control over the process makes them indispensable in modern manufacturing.
Co-Rotating Twin Screw Extruder's Advantages Over Single Screw Extruders
Enhanced Mixing Capabilities
One of the primary advantages of co-rotating twin screw extruders is their superior mixing capabilities. The intermeshing screws create a kneading action, promoting thorough blending of materials and resulting in a more consistent end product.
Increased Processing Flexibility
Compared to single screw extruders, co-rotating twin screw extruders offer enhanced processing flexibility. The ability to adjust screw speed, temperature, and other parameters provides manufacturers with greater control over the production process.
Higher Throughput Rates
The dual-screw design allows for higher throughput rates, making co-rotating twin screw extruders ideal for large-scale production. This efficiency is particularly advantageous in industries where high volumes of material need to be processed within a given timeframe.
Maintenance Tips
Regular Cleaning Procedures
Proper maintenance is crucial for the longevity and optimal performance of co-rotating twin screw extruders. Regular cleaning procedures, including purging and flushing, help prevent material buildup and ensure the extruder operates at peak efficiency.
Screw and Barrel Inspections
Periodic inspections of screws and barrels are essential to identify wear and tear. Any signs of damage or degradation should be addressed promptly to prevent disruptions in the production process.
Lubrication Requirements
Maintaining the appropriate lubrication levels is key to reducing friction and preventing premature wear of moving parts. Lubrication schedules should be adhered to, and high-quality lubricants should be used for optimal results.
Choosing the Right Co-Rotating Twin Screw Extruder
Selecting the appropriate co-rotating twin screw extruder is a critical decision that significantly influences the efficiency and quality of your manufacturing process. With a myriad of options available in the market, understanding how to make the right choice is paramount. Let's delve into the key considerations for selecting the ideal co-rotating twin screw extruder for your specific needs.
1. Material Type Considerations
Different materials have distinct characteristics and processing requirements. Consider the nature of the material you intend to process, including its viscosity, temperature sensitivity, and any unique features. Ensure that the extruder you choose is well-suited to handle the specific properties of your materials.
2. Throughput Requirements
The throughput capacity of an extruder is a crucial factor in determining its suitability for your production needs. Evaluate the volume of material you need to process within a given timeframe. Choose an extruder with a throughput rate that aligns with your production goals, ensuring optimal efficiency.
3. Customization Options
Co-rotating twin screw extruders offer a range of customization options. Manufacturers often provide different screw configurations, barrel designs, and other features that can be tailored to your unique requirements. Assess the customization options available and choose an extruder that can be adapted to meet the specific demands of your manufacturing process.
4. Consideration of Energy Efficiency
In today's environmentally conscious landscape, energy efficiency is a critical consideration. Assess the extruder's energy consumption and opt for models designed with energy-efficient features. This not only aligns with sustainable practices but can also lead to long-term cost savings.
5. Maintenance Requirements
The maintenance demands of co-rotating twin screw extruders vary. Consider the ease of maintenance and the associated costs. Look for extruders with user-friendly designs that facilitate regular cleaning, inspections, and lubrication. A well-maintained extruder ensures consistent performance and extends its operational lifespan.
6. Technological Advancements
Stay abreast of the latest technological advancements in co-rotating twin screw extrusion. Manufacturers often introduce innovations that enhance process control, automation, and overall efficiency. Choosing a model with the latest technological features ensures that your facility remains at the forefront of extrusion capabilities.
喜欢我的文章吗?
别忘了给点支持与赞赏,让我知道创作的路上有你陪伴。
发布评论…